The use of plastic parts is something prevalent for each individual. These plastic parts are not just used in the aerospace industry, medicine and automobiles, etc., but they also have significance in daily lives.
It is significant for each plastic part to have a uniform wall thickness. Wall thickness is normal and achieved in every aspect; however, focusing on its uniformity is also a significant aspect to look at.
If the wall thickness is not uniform, the purpose of that particular part may get hindered. Also, a deformity in part may cause it to break down sooner or later. There is no room for negligence when it comes to uniformity in wall thickness in the case of appropriate injection molding.
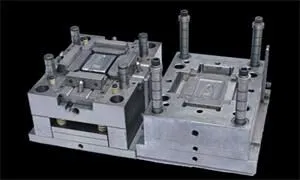
A few essential aspects may be of much help to achieving uniform thickness.
Injection molding is an extensive process and requires effort; at one time, many products are manufactured, and if the walls are not appropriate, the entire effort and cost go down the drain.
Therefore, when it comes to injection molding, a lot of focus shall be placed on the ways that help make the object’s walls thick and uniform. If this is not taken into account, the entire production of the parts may turn out to be deformed.
A few critical factors to be taken into account in case of injection molding to achieve a uniform thickness of wall may include the below-suggested ones:
- The walls of the plastic part must at least be 40 to 60 percent of the adjoining walls. The thickness range of the walls is highly dependent on the material and must fall under the required range.
- Every plastic part would have sharp ends, geometric curves and areas where support spans are needed; this shouldn’t be designed poorly.
- Plastic parts with walls with a good height will need ribs to have strengthened support.
- The guidelines of molding designs should be followed correctly, which helps avoid sinking walls.
Choose Materials Considering Wall Thickness
Material selection is one of the most significant concerns that must be considered. The thickness is highly dependent on the kind of materials chosen for injection molding. Also, the kind chosen varies from the kind of part you must have been designing.
Attributes to consider for wall thickness
Before the material is selected, a few things to consider about the required injection molded part of plastic should fall under an analysis of the following attributes:
- Assess whether the final product you will be manufacturing would be subjected to any chemical or UV rays?
- Know whether the final product will have to pass through extremely high temperatures or not.
- Analyze the strength requirement of the part, and assess whether it would be subjected to heavy loads or not.
- If working on a colored part, assess whether it is capable of being painted or would you have to add color to the resin while the process is being conducted.
- Assess if the optical properties are needed in the finished product.
- Check whether the final products would be used in association with electromagnetic waves in some way.
Focusing on the material family
Sometimes, certain final products also demand a complete switch in the material family to ensure the uniform wall thickness. A few such aspects have been discussed below:
- If you compare acrylic and polycarbonate, you would observe that optical parts are usually made with polycarbonate but keeping in mind the properties of acrylic of not sinking or having bubbles makes it a more practical choice.
- Liquid silicone rubber, suitable for optical grade usage, is an excellent quality option since it allows clarity of the products and ensures light transmission.
- Instead of polycarbonate and ABS, a material called K-resin may also be substituted for its utmost properties, especially when components of the final product are in large size.
- If thin walls are needed for a finished plastic product, one may opt for liquid crystal polymer; it has the properties of a glass filled structure and offers an acceptable use.
Depending upon the required thickness and adding ease and perfection to the manufacture of finished products, these suggested choices may be utilized. These may add a lot of perfection to the final product and help avoid defects.
Clever Tweaks Can Help Strengthen Walls
To strengthen the walls of finished products, one may also play cleverly in the case of the geometrical aspects of the finished product.
More significant areas of cross-sections are not suitable for manufacturing products having the shape of a dumbbell or even bobbins. When cross-sections are removed, the covering strengths and the final products offer to have a proper uniform wall.
Doing this would add strength to the final product and lead to avoiding the sinking of the product, which is one of the most critical concerns of manufacturing products with injection molding. If there is no sink in the product, it is said to have uniform walls.
Also, if the product to be manufactured involves a box-like structure, ribs and gussets may be introduced to it. This will provide additional support to the product, and the criteria of following the 40 to 60 percent of adjacent walls may also be taken into account.
By choosing this method in injection molding, the hassle of shadowing on the walls will also be eliminated. This is caused when parts tend to cool down at different intervals after the process.
Design for Manufacturability Offers Feedback
There are so many challenges to consider when it comes to manufacturing plastic parts injection molding. To achieve the right products to be in place, it is imperative to have good feedback.
Even though the final product is ready with all the rules followed, still there might be some defects that require to be fixed. There is a need to refer to an expert to achieve this aspect. Also, clients may suggest some changes and improvements too.
It is essential to make these changes and also, before making them assess how these corrections appear to be. This all requires feedback from clients that will help in improvements.
Feedback provides room for improvement, and after receiving the quoted part, when a client reviews the products and shares the feedback, a room opens up for improvement. The design may need changes on the part of gate locations and parting lines, and there may be a need to draft angles.
Uneven gate locations, shear stress, and lack of uniformity in walls cause issues with appearance and impact the usability of the product. If the structure is not up to the mark, there is a chance that many problems will be faced when it is put to purpose.
Hence, the role of feedback is significant and allows for making improvements for future production. The injection molding process itself is a complex one and tends to improve with time and practice.
Mistakes to Avoid in Designing for Injection Molding
Plastic parts made out of injection molding need to be very accurate. If made on the part of the process, a single mistake may cause the entire process to go down the drain. Hence, a few mistakes that must be avoided at all costs are fundamental, discussed here.
Non-Uniform Walls
In injection molding, the liquid plastic is poured into the mold and is left to cool down. Commonly, some areas would cool faster than others, bridging a gap between the parts of the same object.
Hence, walls need to be uniform, and non-uniform walls are a significant concern of injection molding and the biggest mistake. This will cause numerous defects like sink area, warping caused due to the stress and will cause a deformed final product.
Therefore, it is essential to make sure that the walls of the part are uniform; this is the thing that must be kept a check when the liquid plastic is poured into the mold. If you don’t look into this aspect, the walls that are thin will cool faster than the thicker ones, and hence a defect would be caused.
Not Utilizing Draft
It is imperative to place a draft angle in the molds before the liquid plastic is poured. If the draft angle is not placed, it could create many problems when demolding the plastic part.
The angle helps in demolding the part correctly, and the absence may cause the part to break while removed from the mold. Hence, it could be a big mistake if the draft angle is not utilized correctly while manufacturing plastic parts through injection molding.
Sharp Corners
The edges of the plastic parts must not have sharp corners. These sharp corners are responsible for causing stress concentration on the rest of the plastic part. It is always best to have the inner radius at least one time to the thickness to reduce the stress concentration.
It is always suggested to make the best use of the above-given tips when it comes to improving injection molding of different plastic parts. The process may seem straightforward, but in reality, it has a lot of technicalities that require considerable attention.
The complex designs, wall thickness and perfection of plastic parts are all interrelated. Hence everything must be done to minimize the defects in the plastic parts. Hence, attention must be paid to the inner and outer radius to avoid sharp corners.
At the Boenrapid, an exceptional level of injection molded parts may be available. An extensive experience in injection molding has made it possible to bring about defect-free and versatile designs of parts that may belong to any industry and be of any complexity.