Die casting uses molten metal under extreme pressure to produce metal components.
It is known that die casting includes a metal manufacturing process where molten metal is injected under high pressure (mostly at 30,000 psi (200 MPa) into the mold cavity. And all the molten metal process is done by a machine known as a die casting machine.
Usually, it is used to achieve the desired shape of metal and has its roots in industrial, automotive, households and lighting, etc.
A number of parts are manufactured via the die casting method including, pistons, connecting rods, electronic enclosures, toys, plumbing fittings, and cylinder beds, etc. There are mainly two methods of die casting: hot chamber and cold chamber.
Cold chamber
In the cold chamber process, Magnesium alloys, Aluminum alloys, zinc alloy, and Copper alloys are used. In a cold chamber, casting machines operated plunger forces a molten to flow in the cold chamber. Cold chamber die casting includes 50 to 90 times per hour.
Cold chamber process:
When the chamber is filled or stuffed with a molten metal then the plunger starts walking forward and makes a pressure compel the metal to run through the sprue into the die cavity.
When the metal becomes solidified, then the plunger goes to its initial place to Receive the new molten metal in the pressure chamber.
Then the die opens and finally, ejector pins remove the casting.
Now the casting cycle can be repeated.
Hot chamber
Hot chamber die casting machines have a short die cycle and they can be used for low malting. In hot hit die casting machines cylinder and plunger are submerged with molten metal in the pot. Hot chamber die casting includes 400 to 900 times per hour.
They create thin-wall casting under precise temperature with a good cavity filling. Maintaining the hot chamber machines is quite expensive compared to cold chamber machines.
Hot chamber process:
The plunger allows the molten to fill the cylinder and die a bit close in this stage.
Then the plunger walks down, forcing the melt by the gooseneck to die cavity.
When the die has been saturated with molten, the plunger holds the pressure until the solidification is completed.
Then the die opens and the casting is Equipped with an ejector.
Then the plunger goes to its actual position and so as the metal residuals back to the top.
Finally, the ejector forced the casting out from the die.
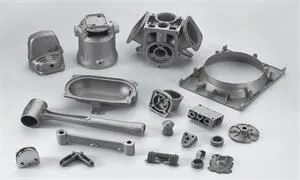
ADVANTAGES OF DIE CASTING:
Easy for mass production
Die casting is made of die casting mold thus can be achieved in specific tolerance and shapes. A little Machining is required and you can produce thousands of identical casting before launching additional tooling. Hence it is quite easy for mass production. Although the initial cost is high but becomes cost effective if you have a threshold of 1,000 quantities.
Dimensional accuracy and stability
Thanks to dying casting, the parts produced by die casting are more stable and durable by maintaining close tolerance. The parts produced by die casting are also heat resistant. Excellent accuracy including die casting tolerance IT13~IT15 in GB/T 1800-2009, and higher precision goes at IT10~W 1 1., along with Surface finish which is 3.2~1.6μm. It saves a lot of Machining cost meanwhile.
Strength and weight
The parts created by die casting are stronger and more reliable than plastic injection molding which also has the same dimensions. As we explained earlier, thin-wall castings are lighter and stronger than other casting methods.
Moreover, die casting does not have separate parts fastened together and or welded, therefore strength is due to alloy rather than joining process.
Economical for mass production
The starting cost may be high but with this cost, you can produce a variety of items. The complex-shaped parts can be achieved with high performance and assembly work reduces. Other materials can be embedded in die casting methods including complex parts. It saves materials cost process.
Variety of surface textures
Suitable for smooth textured parts as well as flawless parts. It offers you diverse flexibility to finish parts in a wide range of technology.
DISADVANTAGES OF DIE CASTING
Die casting has plenty of advantages, it also has some drawbacks. In this section we will explain the disadvantages of die casting. The disadvantages are few as compared to the advantages.
Low die life
During the high melting point, some metals such as copper alloys have a high melting point and also it is not suitable for small products.
Large capital investment
Die casting machines cannot accomplish their task without dies and related equipment comparison with other die casting processes. As a result, if die casting is necessary then large mass production should be at the top priority due to the high cost of dies, and other equipment. Large parts cannot die and take a long lead time.
Porosity generated easily
If the air evacuation from the die cavity is not sufficient and proper it can cause Porosity. Therefore, special precautions are required for the die casting method. Otherwise, there is the risk for other gasses to entrapped
The different types of die casting:
Gravity die casting
Aluminum die casting
Structural die casting
Pressure die casting
COMPARISONS WITH OTHER PRODUCTS
As compared to other manufacturing methods, die casting has its unique advantages over other methods:
Plastics injection moldings
Comparison of die casting with injection molding can be observed with unique features of die casting, as parts of die castings are more strong, harder, more resistant to heat, more dimensionally stable, and superior to plastic in respect of cost and performance.
Moreover, die casting is durable under load, resistant to UV, stress cracking, and weathering in all conditions. The production process is much faster than that of plastic injection parts.
Sand castings
And compared to sand casting, die casting parts need less processing. A part created with die casting has thin walls, maintainable in tight dimensions, and has high production efficiency.
Moreover, the surface of the part is smoother and needs low labor costs as well. On the other hand, sand casting can take ferrous and non-ferrous metals to produce parts and these alloys are not suitable for die casting.
Forgings
As compared to forging, die casting has the following advantages…
complex in shape and has shaped not forgeable
have thinner sections
closer dimensions
coring not feasible in forgings
On the other side, Forgings are stronger and denser than die casting and have wrought alloys properties. It is produced in ferrous and other metals and is not suitable for die casting due to its size.
Stampings
As compared to stampings, you can replace one die casting with several parts, as die-casting needs fewer assembly operations, and you can hold it closer to dimensional limits, while Stampings have wrought metals properties and can be created in alloy or steel but not for die casting. In simple form, it is produced rapidly and has less weight than that of die casting.
Who uses diecasting?
Not your business can get an advantage from die casting, think again, there are a number of industries that use die casting processes to get high-quality physical parts and save money. Below mentioned industries use die casting for their benefit.
Automotive die casting
The automotive industry is one of the biggest industries of our time, it demands high durability and strength. No doubt, the die casting process can give the best high-quality parts to the automotive industry.
Medical devices
Everything in the medical field be it patient bed or doctors equipment, everything uses a die casting process.
Lighting and electrical
We work with supermarkets, event management, and commercial clients to meet the electrical requirements and specific lighting.
Defense
As all the countries are growing their military equipment and making their defense system strong and strong. In this regard die casting is providing strong and durable military equipment.
Conclusion
Die casting products are widely used today. Die casting has its unique role in the production of laptops, cameras, mobiles, motorcycles, and automobiles. It has its unique advantages and disadvantages over other methods.
I hope the information would be informative, Bohao prototype not only offers die casting services to meet your production projects but also the best in rapid injection molding as well as vacuum casting.
We use industry-leading technologies to provide high-quality die casting. We want you to contact us if you want to run your die casting project successfully, and we would give you professional services and advice for your next project! Be confident and give us a call.